把专家知识的价值带给客户
12 12月 2019 阅读时间 计算文字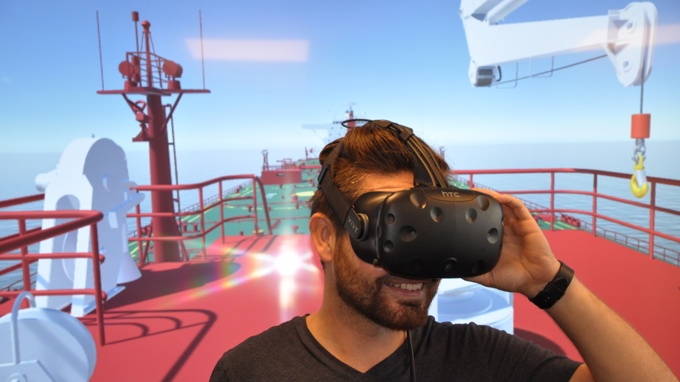
The environment is virtual, but the expertise is real; MacGregor’s Jan Finckenhagen and Floor Meijs explain how virtual reality crew training can make complex operations safe and efficient
Effective crew training is essential within the offshore industry, with some elements being a mandatory requirement and other courses aimed at optimising onboard safety, efficiency and equipment reliability.
However, not all training offers the same capacity for in-depth learning and fully immersive, virtual reality training proving valuable to customers seeking to maximise the operational benefits of MacGregor equipment and systems.
The development of simulation software for mission-critical equipment is undertaken in close liaison with our design and technical departments, which then ensures that training in a virtual environment is as realistic as possible and delivers the intended commercial benefits.
For example, bow-loading system transfer of crude oil between production units and shuttle tankers is environmentally sensitive work and highly regulated. It is consequently a legal requirement for crew to receive training prior to operating such equipment, even if they have been working at sea for many years. Here lies the advantage for an operator because there is a material difference between conventional classroom-based teaching and virtual reality training.
The more realistic the training, the greater the depth of learning. By undertaking virtual reality training, every possible operational scenario can be simulated, including weather and sea state changes; all mimic operational conditions enough for a participant’s brain to perceive that the environment as real, which is key to learning. Emergency situations which cannot be fully tested onboard can be simulated, as well as maintenance and troubleshooting. This reduces the likelihood of injury or equipment damage because proper operation has been tried and tested in a risk-free environment.
Personnel from different companies, with varying degrees of experience, attend the courses that we facilitate and share their knowledge, which also brings a unique contribution to the training.
Capable crew create additional commercial value
The primary objectives of all virtual reality training programmes are to optimise equipment use, minimise errors and avoidable damage, and enhance service and maintenance capabilities. Accidents mostly happen because of unfamiliarity with equipment and unpractised routines. Within a virtual environment, crew can quickly and safely gain equipment-specific and operational familiarity prior to going onboard.
MacGregor has established a state-of-the-art training facility in Arendal, Norway which is divided into two zones:
- An offshore crane simulator including an operator’s chair and portable remote control, which behaves in exactly the same way that it would onboard;
- A zone where participants can walk around the simulated ship, familiarising themselves with safe operation of the installed equipment. The use of ‘real’ equipment in practice exercises provides huge potential for knowledge transfer.
The system software is linked to an advanced simulation platform called ‘C-HOW’. Digital copies of equipment are created, and customer-specific operating scenarios and hazardous and unusual situations can all be simulated and trained on.
As part of further progressing the training programme, we are also developing a virtual reality function that can be used for predictive purposes during operation. This uses our extensive operational knowledge to create ‘what if’ scenarios and the ability to manage them effectively, enabling personnel to make better decisions and execute tasks in an optimal way.
Positive impact on equipment maintenance
Customers gain troubleshooting and maintenance knowledge as a result of their training experiences. Feedback from customers and our own service departments demonstrates that crew who have attended these courses have improved their operational knowledge to such an extent that they no longer call us for minor troubleshooting and service issues.
With more effective training, the value for the operator is that the crew onboard can repair the things they are supposed to repair, with MacGregor service personnel only travelling to undertake complex tasks where our expertise is used more effectively.
Virtual reality training is a time-efficient way to train crew and establish high safety and efficiency standards prior to the vessel leaving for offshore operation. It can save days, if not weeks, of time in comparison to conventional classroom and onboard training methods, enabling the operator to focus on the vessel’s primary purpose whilst at sea.
Building a virtual future
In the future, operators wishing to have more control of their own knowledge and crew training will be able to take advantage of portable virtual reality systems.
We recognise that the most powerful, deep-learning experiences are to be gained through a combination of training opportunities, encompassing immersive sessions in our facility that are then augmented through the use of portable systems in customers’ own facilities.
Enormous scope remains to develop virtual reality capabilities even further and we are only just beginning to explore its full potential through interaction with our customers, with requests to do so steadily increasing.
Notes to editors
Jan Finckenhagen, Training Manager, Offshore Solutions Division, has worked on vessels all over the world as a Service Engineer. In 2014, he moved to the development and delivery of training solutions that make the most of expert knowledge transfer through new technologies. He has more than a decade of experience with MacGregor and is well-placed to ensure that crew realise their training potential which, as a result, maximises an operator’s return on investment.
Floor Meijs, Senior Manager, Digital Solutions leads MacGregor’s C-HOW simulation team. She is a Master Engineer and joined MacGregor earlier this year to apply her knowledge of developing intelligent solutions from a design and usability perspective. Over the past ten years, the core focus of her work has been on how equipment suppliers can harness intelligent functions within their products and offer this expertise to customers.